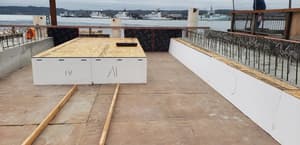
The Newport Warf project, located in Newport, Oregon, was constructed in 2020 using a patented system of EPS form liners to form the horizontal surface of the wharf positioned on top of the 48” wide pile caps.
After construction of the 24 inch diameter pilings and the 36 inch thick 48 inch wide pile caps were completed, horizontal formwork was set up for the final concrete installation.
First the contactor installed the horizontal platform which acted as a working surface as well as support for the horizontal EPS (expanded polystyrene) form liners. The EPS form liners consisted of 323 blocks of EPS15 Geofoam in various sizes with 7/16 inch OSB attached to the top and some of the sides. The OSB was attached using a patented system Universal Foam Products developed where slots are cut into the EPS 2 inches below the surface and OSB strips are inserted. Then either plywood, or in this case 7/16 inch OSB panels are attached to the EPS by running screws into the strips embedded in the foam. This attaching system is more secure than adhesives and also makes it easy to remove the OSB or plywood panels so they can be repurposed. The OSB was attached at the factory so the panels were ready to install as soon as they were delivered to the site. There were seven different configuration of panels, all clearly marked for easy identification.
Concrete form liners of EPS are used for a variety of construction applications where curves, angles or patterns are required making other alternatives very expensive. Some applications include both vertical and horizontal bridge supports, imbedded patterns in concrete retaining walls and tunnel entrances, as well as waffle forms for parking garage decking. Universal ships form liners from facilities throughout the country.