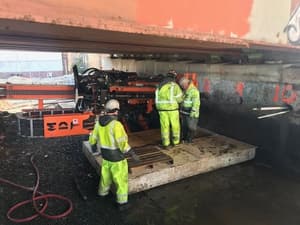
EPS15 Geofoam is light enough to easily move around and strong enough to handle the kind of abuse provided on a construction site.
Our customer was contracted to install tiebacks through an existing concrete abutment. They needed to excavate far enough below the bridge deck in order to fit their drill rig on each location. The foam blocks were required so their crew could work the front of the machine at a reasonable height and give them firm ground to stand on, two concerns alleviated by the
EPS15. The crew was able to move the blocks by hand. Given the limited access for any support equipment this was a major factor, so they would set the drill rig on location, set up the foam blocks with the required tooling, drill to the required depth, set the reinforcing steel and grout the hole/anchors all while on the blocks. They installed 10 anchors under this bridge.
On a second project, they were contracted by the MBTA to stabilize a failing retaining wall. They placed a thin layer of shotcrete on top of the existing concrete retaining wall, then drilled soil nails through the shotcrete to a depth of 20’ behind the face wall. In this picture they are testing the soil anchors by “pulling” on the thread-bar to make sure the design loads are satisfied. They used the foam blocks again as a platform for the crew to safely work off of. The jack that is behind the plate on the wall weighs about 100lbs, so not something you can lift over your head easily. The blocks allowed two workers to set the test set up at a reasonable height. Directly behind them was a live train track. Utilizing the blocks allowed them to quickly break down the platform, which had to be done 1 to 2 times per night.