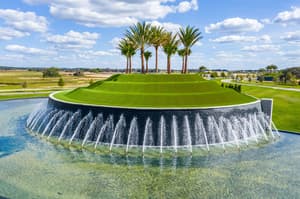
The fountain project that The Rogers Group is working on. They used EPS 15 Geofoam to create the taper for the stone wall that will be the backstop for the water shooting against it. There are 7 fountains total in this project and the combined linear footage of the fountain walls is approximately 1140 lf. When it is all said it done this will be a Crystal Lagoon Community.
EPS Geofoam
Geofoam is a lightweight void fill material that is the preferred
building material in a large variety of construction applications. The
advantages of EPS Geofoam over other fill materials are significant.
1.Weight
A cubic yard of crushed stone weighs 2,800 to 3,000 pounds per cubic
yard. A cubic yard of soil weighs 2,000 to 2,200 lbs per cubic yard.
Sand weighs 2,700 lbs per cubic yard.
EPS Geofoam weigh between 19 pounds and 81 pounds per cubic yard depending upon compression strength requirements. The light weight and high compression strength make it an ideal fill when poor soil conditions exist, and additional loading is not an option.
2.Compaction
Common fill materials such as stone, earth and sand all require
compaction and continue to settle somewhat over time. EPS Geofoam does
not require any compaction, thus reducing overall installation time. It
is delivered to the jobsite in large blocks ready to install.
3. Installation
Geofoam blocks for large earth fill projects are typically 36” x 48” x
96” or larger, weighing between 87 and 274 pounds each, depending upon
density. They can be easily moved around on site by hand, or with
lightweight backhoes and cranes, eliminating the need for heavy earth
moving equipment for this part of the project.
4. Cost Savings
Although the material cost of EPS Geofoam may be higher than that of
other common fill materials, the reduced installation cost can be
substantial enough to make the installed unit cost less than other
materials. There have been large projects where geofoam was chosen
primarily due to the speed with which it can be installed compared to
other fill materials. This accelerated installation equates to less
labor and shorter disruption of the area around the construction site.
5. Historical Data
The first highway project using EPS geofoam was done in Norway in 1965.
The first bridge abutment project using EPS geofoam, also in Norway, was
in 1972. Since then, thousands of civil projects have been completed
using EPS geofoam worldwide. Since the first projects were completed,
the manufacturing process has improved, testing has become more
sophisticated and factories can mold larger and denser blocks, creating
even more opportunities.
Initially skeptics wondered if geofoam would maintain its composition and compression strength long term after being buried in the ground for years. Excavated samples from both the highway and bridge project in Norway years after construction showed that there was no decomposition and the compression strength was equal to or greater than when the blocks were installed. Tested samples from multiple projects in the US have confirmed these findings.
Applications
Construction over poor soil conditions
If a highway, parking lot or structure need to be constructed in an area
with soft or marginal soil conditions, EPS geofoam may be the solution.
Removing soft clay or sand and replacing with geofoam can reduce the
load on the underlying soils substantially. By removing 10’ of clay
weighing 2,000 lbs per cubic yard and replacing it with EPS29 geofoam
weighing 49 lbs per cubic yard you have a net difference of 722 pounds
per square foot on the underlying soils. The EPS29 geofoam has a
compression strength of 10.9 psi at 1% deformation (1,570 pounds per
square foot).
Bridge abutments
The first use of EPS geofoam to reduce the lateral load on a bridge
abutment was in Norway in 1972. Since then, that same application has
been used in the construction of bridges around the world. By placing
geofoam blocks in increasingly wide layers moving away from the bottom
of the structure, the lateral loads of earth can be substantially
reduced.
Slope stabilization
Unstable slopes can be costly to maintain as well as a public hazard.
One of the main causes of slope destabilization is the weight of the
soils. By replacing soils with lightweight EPS geofoam, that problem is
reduced with a properly designed solution. EPS geofoam, when used as a
part of an overall slope stabilization plan, can eliminate future
deterioration of the area.
Backfill against retaining walls
A primary consideration in the design of a retaining wall or ERS (earth
retaining structure) is how the lateral pressure of the earth against
the wall impacts the cost of the structure. Installing EPS geofoam, in
layers, at approximately a 40 to 50-degree angle away from the base of
the ERS will reduce that lateral pressure, in some cases allowing for a
more economical wall to be constructed. The design & cost of the geofoam
placement and the cost savings in the construction of the ERS are both
considered in the design analysis.
Protection over utilities
Buried utilities often pose a problem for construction. Damaged
underground utilities can be costly; disrupting essential services,
requiring emergency repairs, creating downtime and possible injury. To
reduce the downward pressure on underground utilities, EPS geofoam is
used. Geofoam can be placed directly over the utilities. It is built up
in layers with each layer wider than the previous one creating a wedge
shape.
Insulation for buried utilities
Freezing water mains are a major problem in many of our older cities
with dated infrastructures. EPS geofoam can be used to insulate over top
of the water lines while supporting the vehicular loads of the roadway
above. EPS geofoam is an excellent insulation material with R-Values
ranging from R-3.3 per inch to R-5.05 per inch at 40° F so besides
having structural integrity geofoam can also help keep buried waterlines
from freezing.
Projects with tight timeframes
Often roadway and other infrastructure projects require short schedules.
Sometimes due to weather or traffic or some pending event a project
needs to be done quickly. EPS geofoam installs fast, without the need
for tamping in small lifts to obtain proper compression strength. A
small crew with a light crane can install geofoam blocks quickly.
Projects with limited space
Building up an area for a roadway or structure with most common fill
materials typically requires a sloped embankment on both sides of the
built-up area. Occasionally there is not enough room for that to happen
due to property lines or utility placement. Geofoam blocks can be
stacked vertically without the need for side slopes taking up
substantially less space.
Compressible Inclusion
One type of geofoam that is unique from all others is a material called
TerraFlex. TerraFlex is a compressible inclusion. It is engineered to
compress and then return to its original thickness. The primary
application for this material is against bridge abutments and retaining
walls where freeze thaw conditions or the potential for seismic
conditions exist. The TerraFlex absorbs the lateral pressure so the
concrete abutment or wall does not need to.
Stadium seating for theaters, churches & lecture halls
Precut blocks of EPS15 geofoam are used to create the tiered seating in movie theaters, churches and college lecture halls. The geofoam, in conjunction with our Leave-In-Place Steel Riser Form System, allows contractors to erect and finish the multiple tiers quickly. A secondary potential benefit is the reduction in sound transmission between rooms.
Reduced weight for raised floors
As building occupancies and uses change, the configuration and elevation
of floors may also need to change. Often these elevations and
configurations need to change without imposing additional weight on the
underlying structure. Some examples of this are a sloped floor in an old
movie theater being leveled for retail space, or a sunken lobby in a
hotel being eliminated. EPS geofoam is significantly lighter than other
common fill such as stone, sand and earth and is much cleaner (and
quieter) to work with indoors.
Swimming pool construction in multi-story buildings
In new multistory residential buildings, swimming pools are often put on
upper levels of the structure. Since the final pool design is not always
completed at the time of construction a rectangular “tub” or “vault“ is
constructed where the pool will be located. Once the final design is
completed the finished pool floor will need to be sloped, fill will be
needed for steps and sunning shelves and the length and/or width of the
space may need to be filled in to adjust to the finished pool design.
EPS geofoam is used in this application because of its light weight and
high compression strength.
Swimming pool infill
Just as EPS geofoam is used in swimming pool construction, it is also
used when a swimming pool is filled in making way for a new use of
space. This can be in a multi-story building or someone’s back yard. The
geofoam can be delivered to the site pre-cut and pre-tapered to make the
fill-in process go very quickly with minimal construction noise. Since
the geofoam typically used for this application weighs less than 1 lb
per cubic foot there is a net reduction in weight placed on the
underlying structure.
Concrete Form Liners
Conventional concrete formwork is ideal for straight runs for walls and
square columns, but when curves or patterns are required, steel and wood
forms can be extremely expensive and often have long lead times. EPS
geofoam form liners are much more economical, attach to conventional
straight forms easily, and can provide very complex shapes for concrete
forming. Because geofoam compression strength is calculated @ 1%
deformation, it is easy to select the best density to use for any
project.